Featured Articles
Most Recent Articles
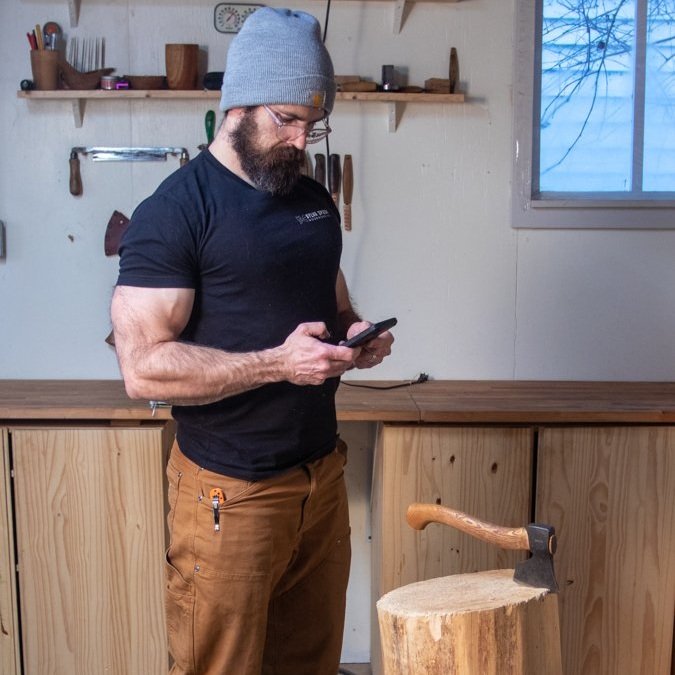
My Social Media Dilemma
Discover my dilemma of using social media as a spoon carver. How can i connect with fellow carvers while balancing the craft's need for focus and mindfulness?
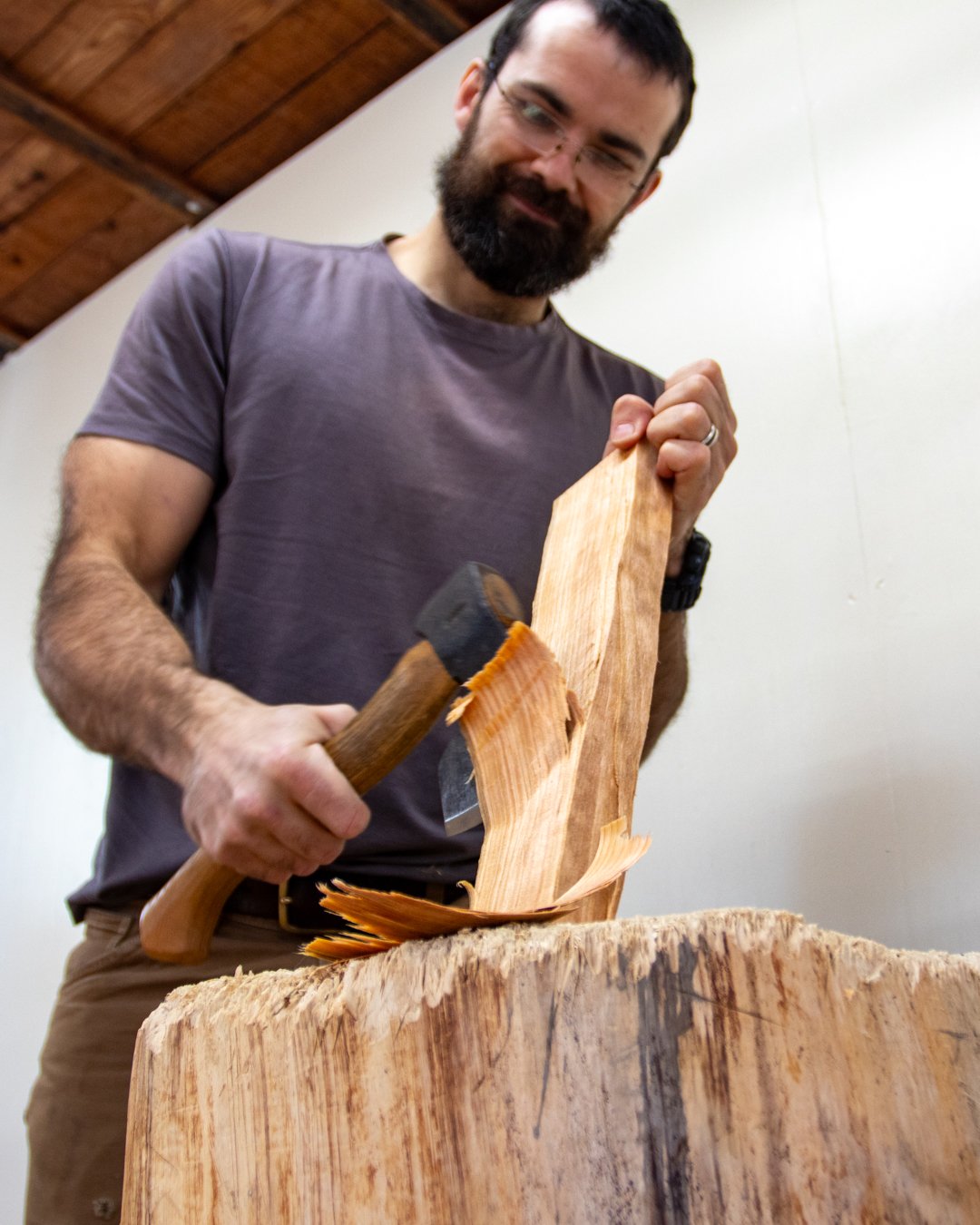
Spoon Carving Trends in 2024
Ever wondered what's simmering in the world of wooden spoons? Dive into the hottest trends reshaping this timeless craft, from daring decoration to sustainable sourcing, here are some of the hot topics you might encounter this year
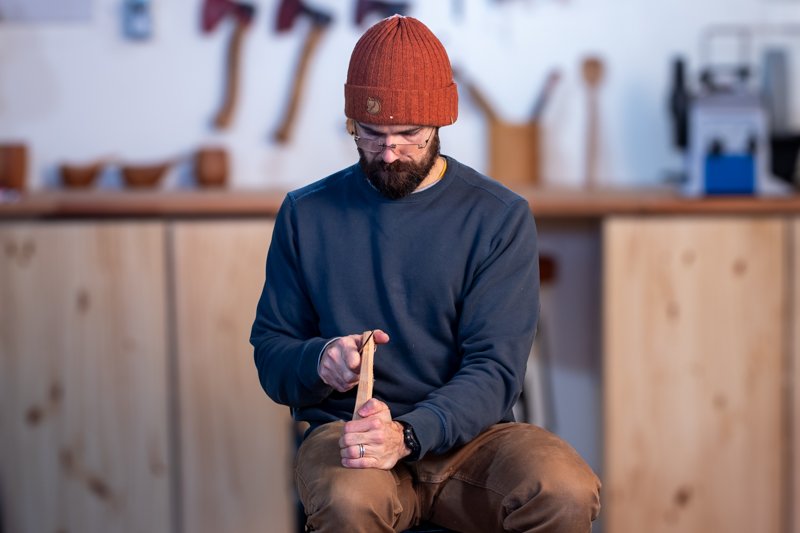
Ditch the Resolutions, Craft a Spoon: Why This Humble Hobby Rocks
New year, new you? Ditch the resolutions and try spoon carving - a rewarding hobby that boosts mindfulness, creativity, and more.
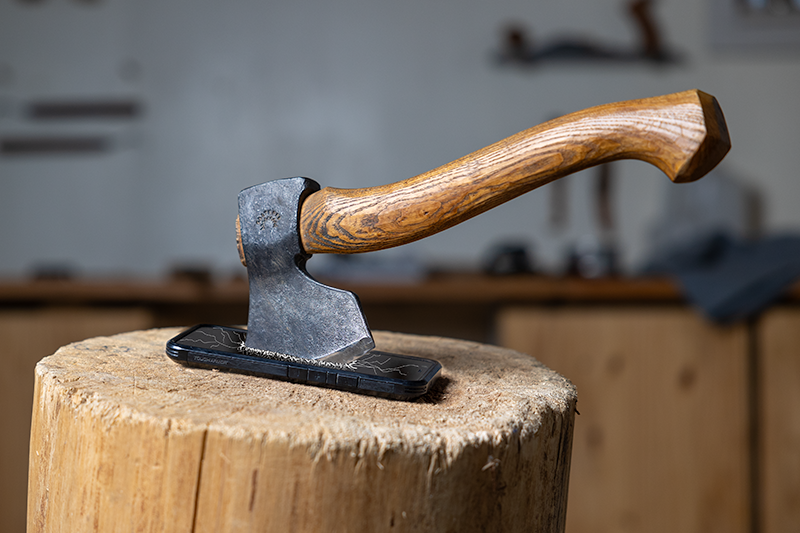
Rediscovering Purpose Through Spoon Carving: A Tech Era Antidote
In an age where our eyes are glued to screens and our minds are bombarded by endless notifications, the craft of spoon carving emerges as a surprisingly profound remedy. This simple yet immersive hobby offers not just a creative outlet, but a path to rediscover our lost sense of purpose in the digital whirlwind of modern life.
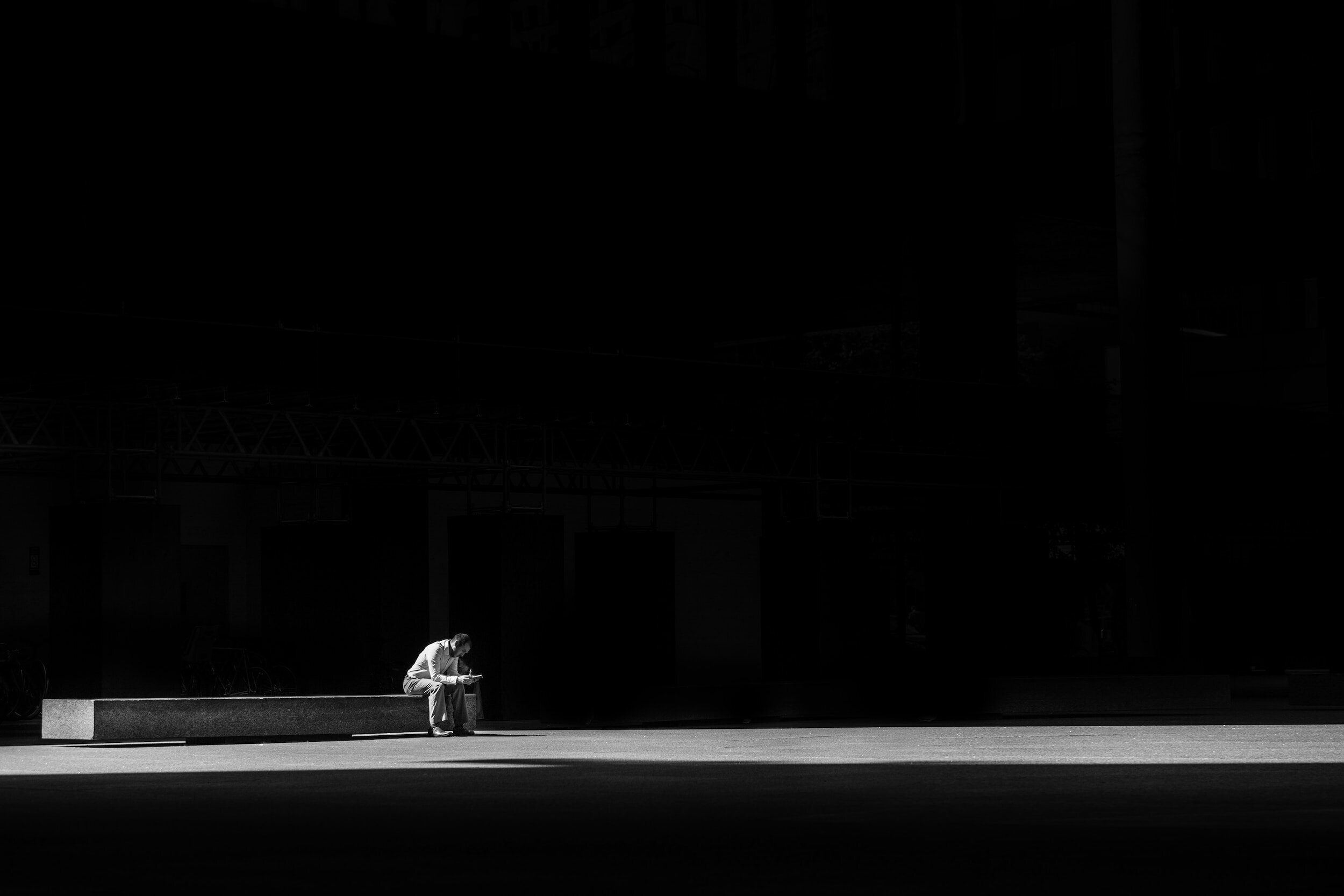
Spoon Carving Is The New Way to Bond with Your Bro
Loneliness is more than just an emotion – it's a health risk, with studies linking it to various serious health issues. While both genders experience loneliness, men often struggle more with seeking help due to societal expectations and biological responses. This blog offers a unique solution to male loneliness: spoon carving, an activity that not only allows men to bond over a shared task but also connects them to wider communities and offers a retreat from the digital world.
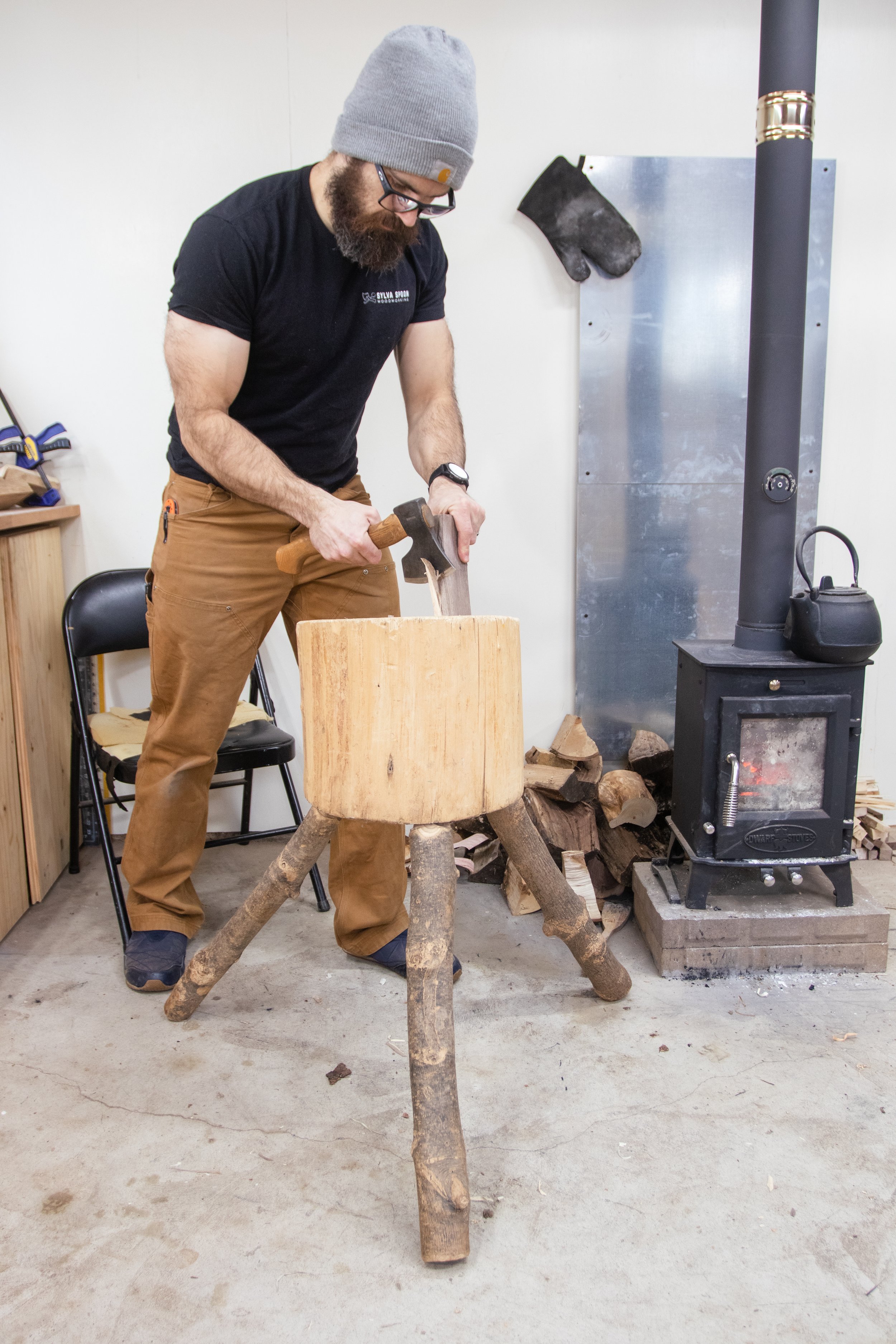
Why Spoon Carving is the Perfect Hobby for Introverts
While the world often celebrates extroverted qualities and social activities, it's essential to recognize the unique needs and strengths of introverts. I’m certainly an introvert. While socializing is enjoyable, I find it draining. I need the solace and fulfillment found in activities that allow for solitude and self-expression. One such activity that perfectly aligns with the introvert's disposition is spoon carving.

The Stoic Wisdom of Carving Wooden Spoons
Imagine two distinct activities: one, delving into the rich philosophies of Marcus Aurelius, an emperor who ruled the world's most powerful empire two millennia ago. The other, carving wooden spoons.
These activities seem worlds apart. But we can find some common threads that aligns the ancient wisdom of Stoic philosophy with the peaceful act of crafting wooden utensils.
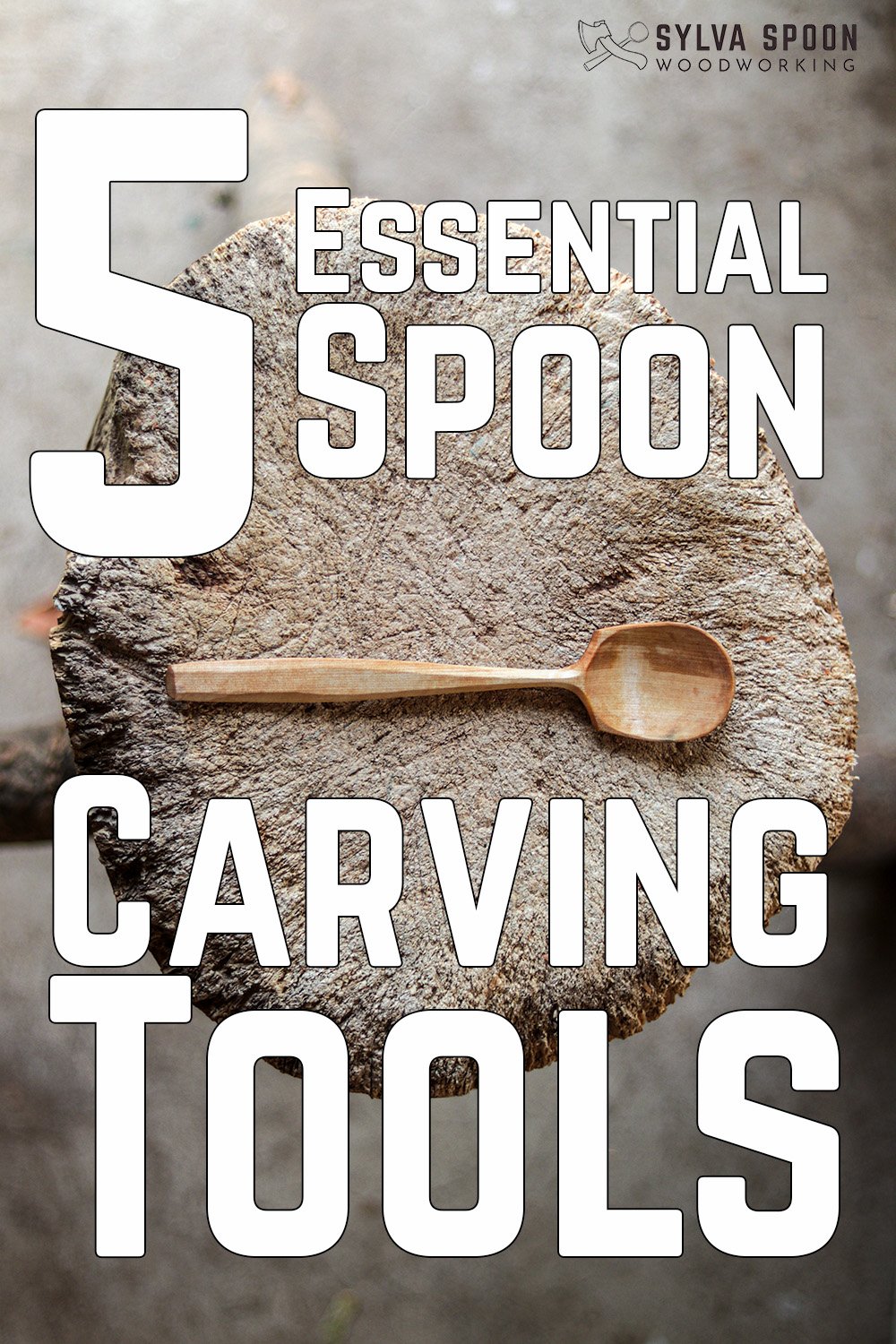
5 Spoon Carving Tools You Can't Live Without
One of my favourite things about spoon carving is the minimal tool kit required. If you buy some spoon blanks all you really need is a straight knife and a hook knife. But these 5 tools are the essentials that should be at the core of every spoon carving kit.
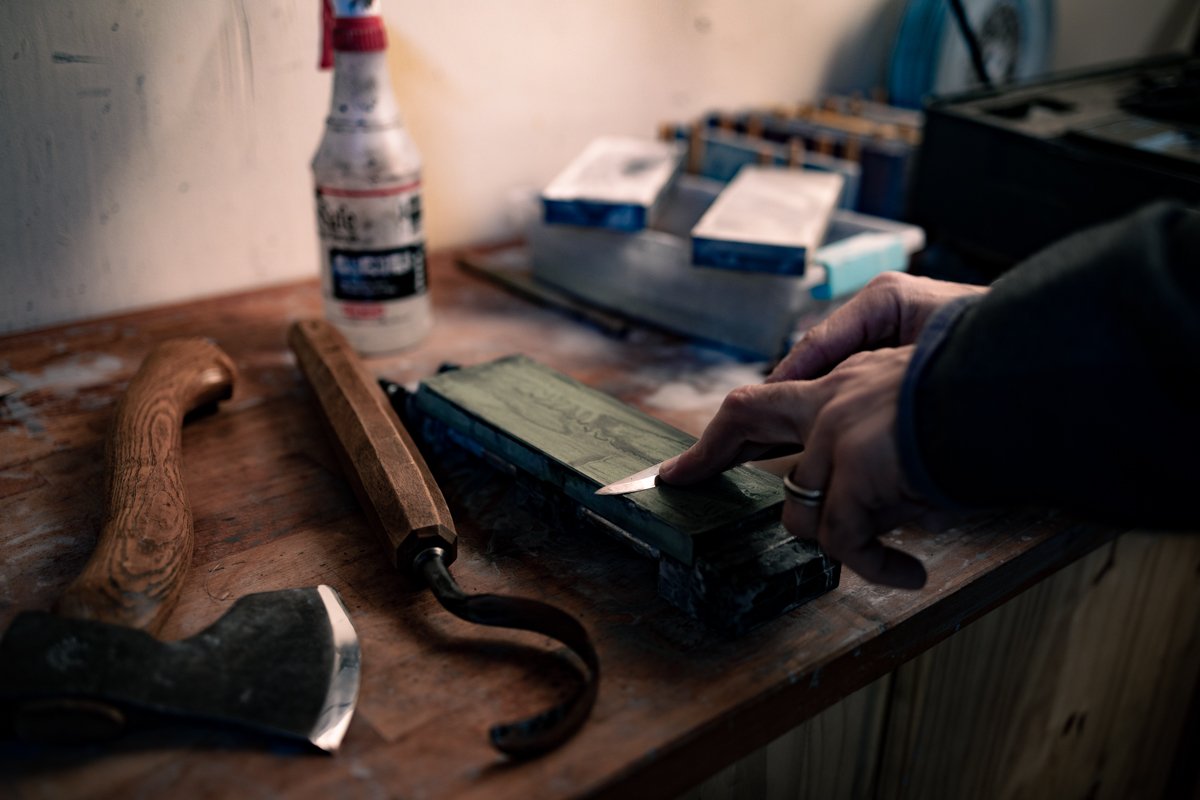
5 Easy Tips To Quickly Improve Your Spoons That Don't Involve Carving
The best way to improve your spoon carving is to carve lots of spoons. Getting the reps in is the fastest route to improvement in any field. That said, here are 5 tips that will help you get more out of your time spent carving.
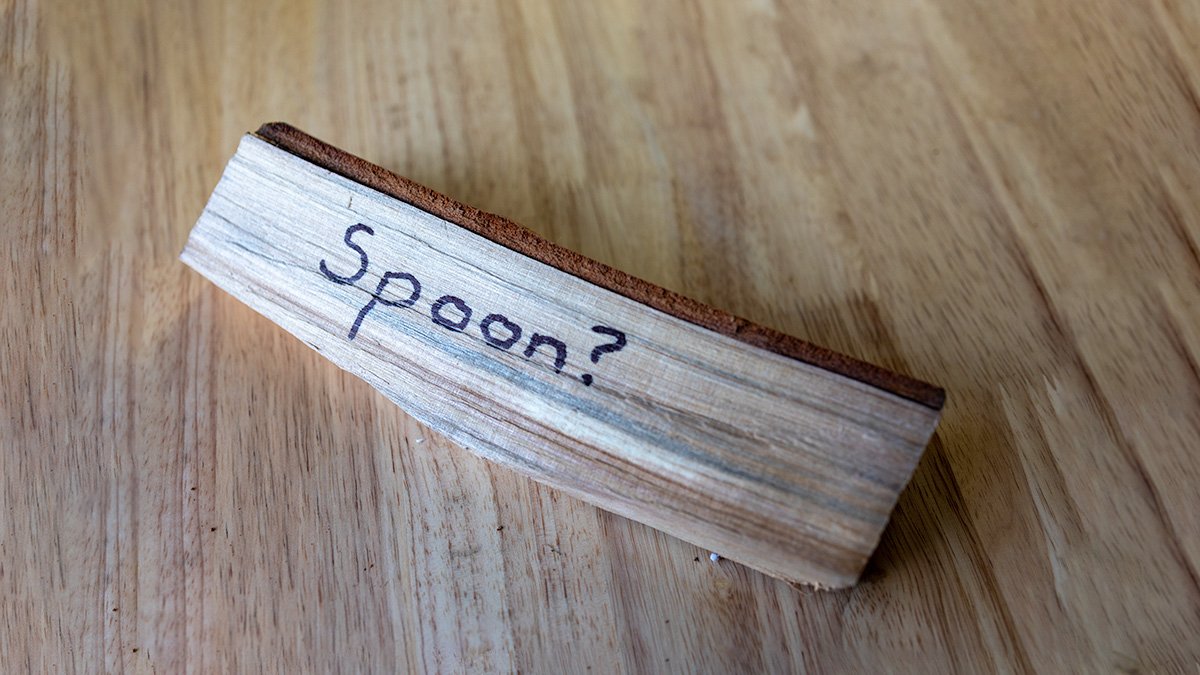
Take One Simple Step To Improve Your Spoon Carving Now
When I started out out, I carved a lot of bad spoons. It took a long time to figure out certain tips and tricks to making spoons that work well. This is tip is one I really wish I’d been told about earlier.
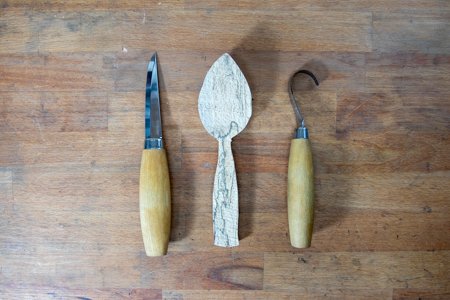
3 Spoon Carving Setups: Beginner, Intermediate and Advanced
Spoon carving is a fantastic hobby. It’s incredibly easy to get started with. It can be done almost anywhere, with a minimum of tools.
Here’s a quick look at what different spoon carving setups might look like.
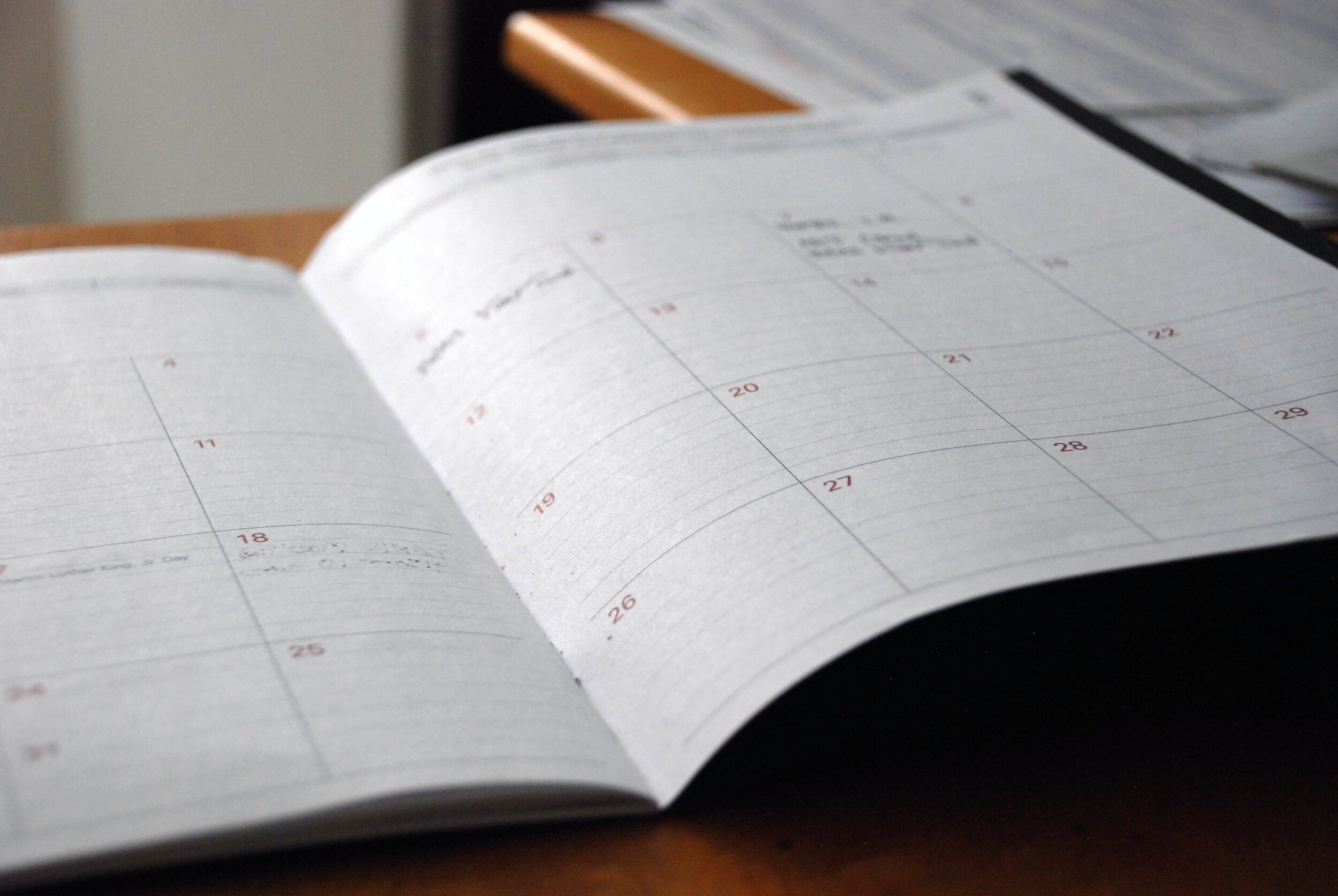
Three Best Strategies To Easily Make More Time For Creativity And Play
You want to make things. You also want to be good at making things. Creativity is a core part of our natures.
I’m quite creative in the sense that I physically create things. However, not so much in terms of originality or imagination. It’s something I want to work on.
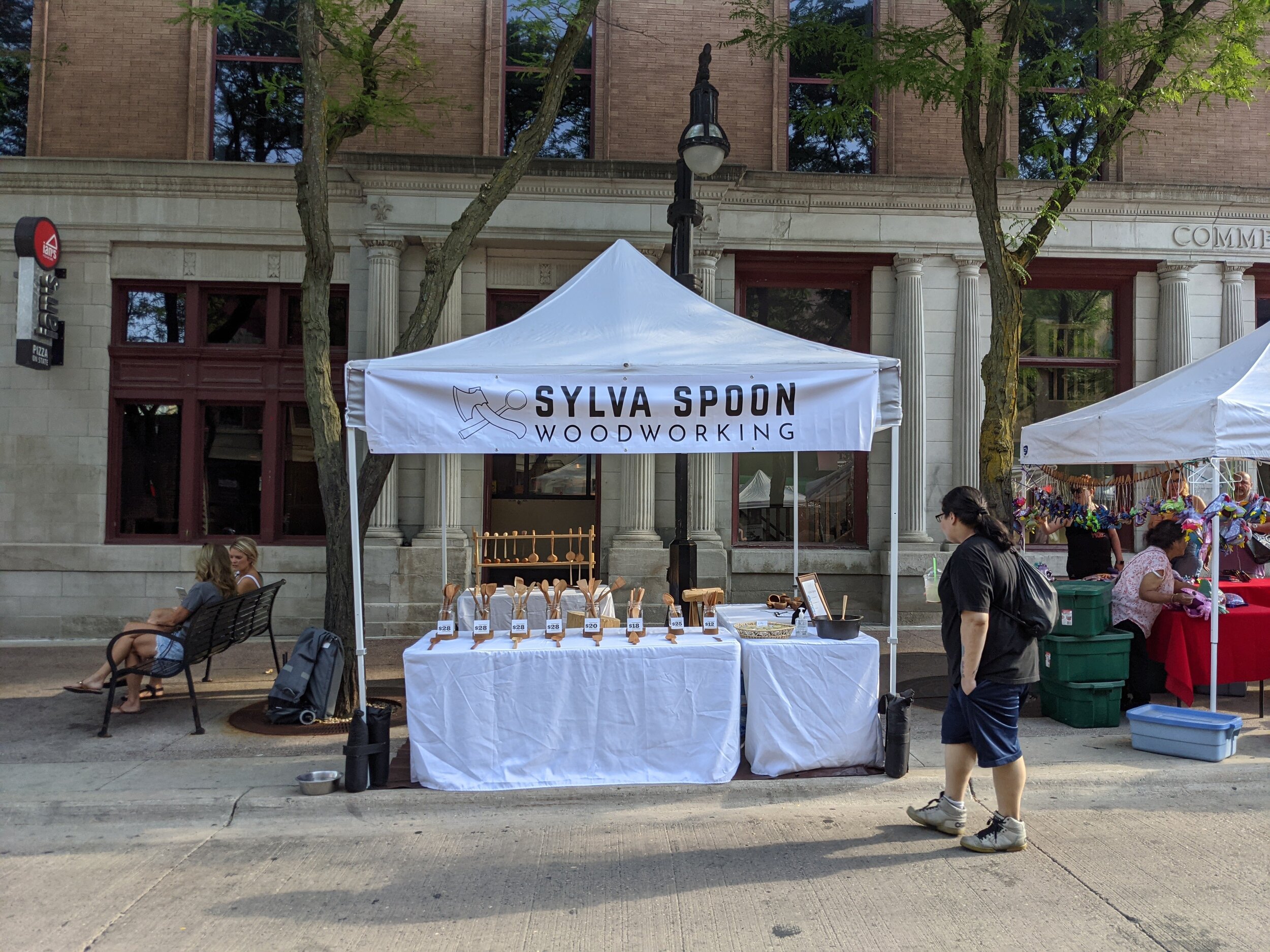
June Update
At the beginning of 2021 I thought Sylva Spoon was going to be entirely online for another year. I spent a some time planning out the physical and digital work I wanted to do and I spent about five months putting that plan into action. Then on June 1st I got an email from the Street Vending Coordinator for the city of Madison. The downtown Farmers’ Market would be returning to the Square on June 19th.
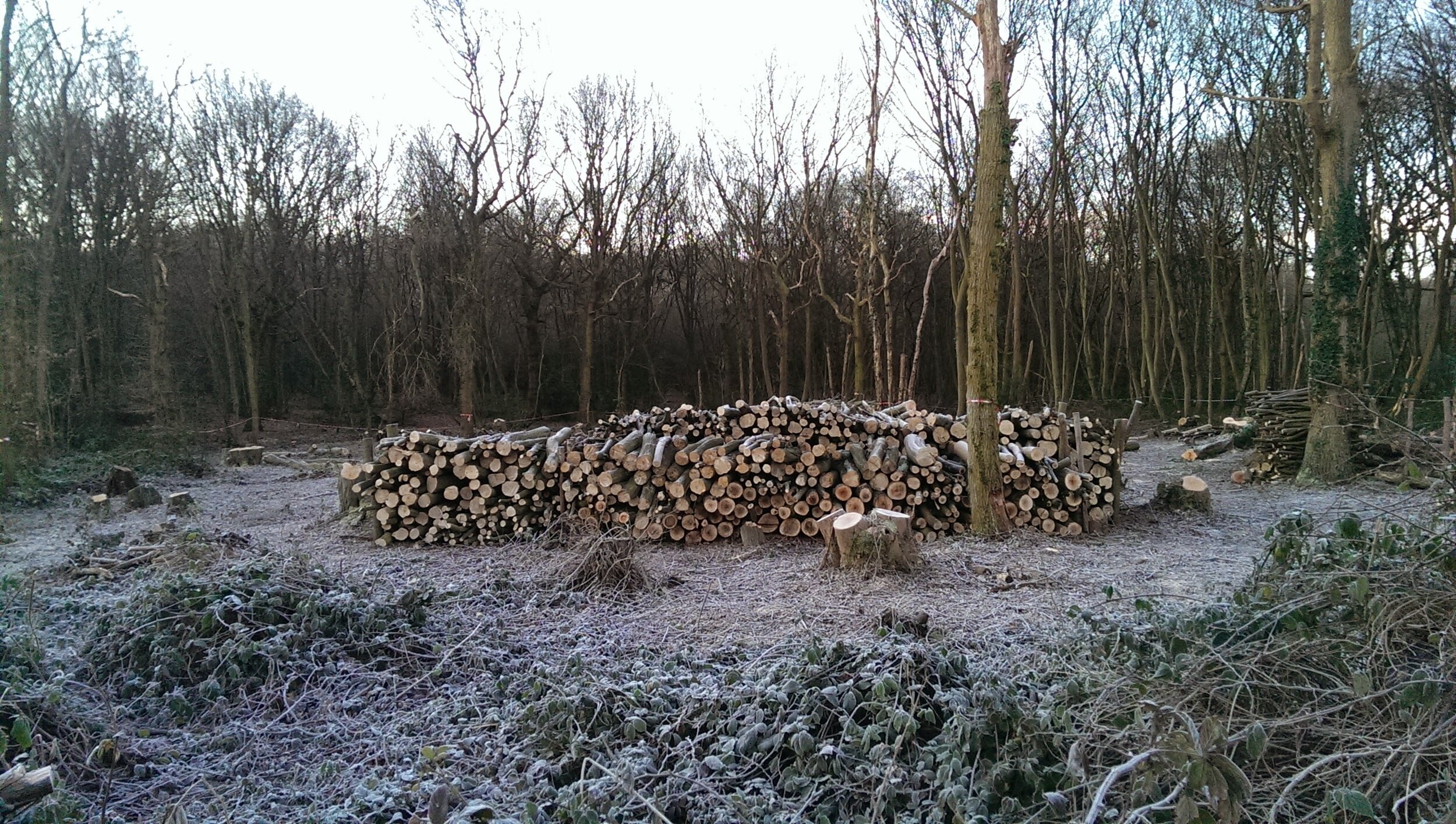
Every Spoon Carver Should Adopt These 5 Simple Rules for Storing Wood
Spoon carving is most enjoyable with green wood. Wood that has a high moisture content. The moment wood is cut down it starts to lose moisture. You want to slow down the drying process, but not have the wood rot. This means you need to be strategic about how you store wood.
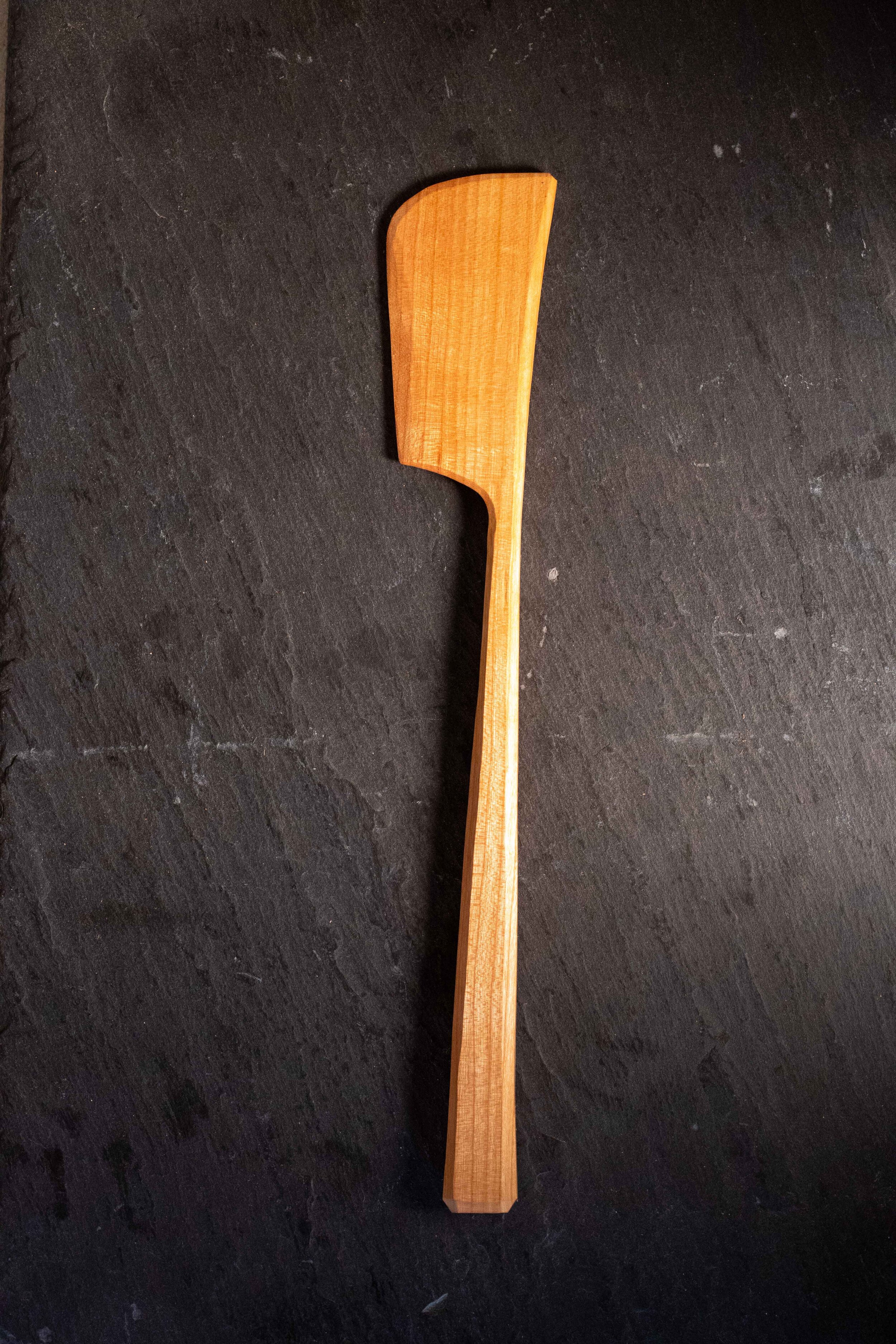
Butter Spreaders Are Easily The Perfect Beginner Woodworking Project
If you're interested making things by hand, the humble butter spreader is a great beginner project. It can be done with found material, using tools you probably already own. Once you're done, you'll have something you can use in your own kitchen.
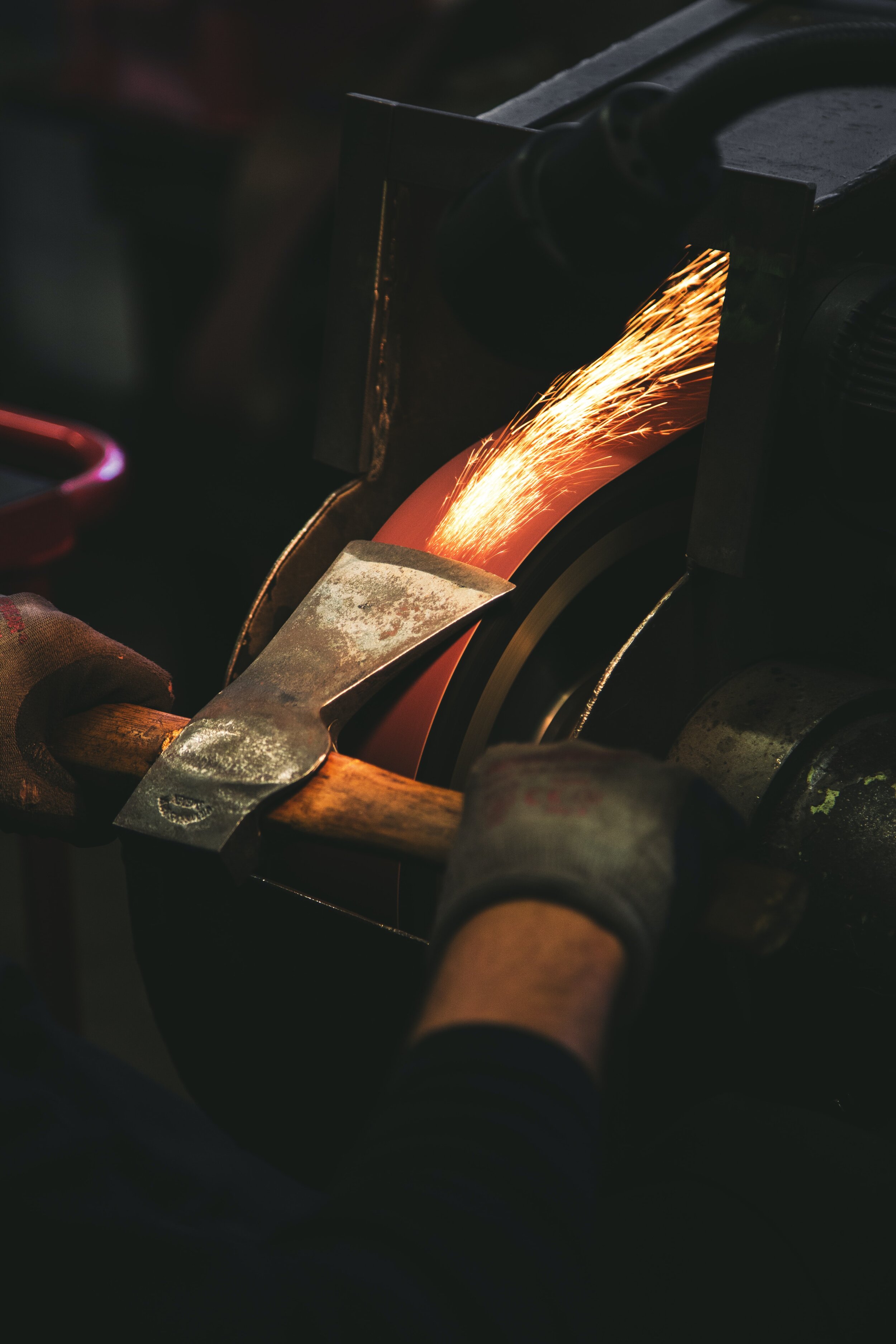
Beware Of These Six Tool Sharpening Mistakes Beginners Make
Lots of folks that enjoy carving don’t seem to enjoy sharpening quite so much. I kind of understand that. These folks are interested in carving, not sharpening. Blunt tools are an unfortunate byproduct of carving. And sharpening is a chore to be endured. That’s completely the wrong mindset. And I’m here to help make it more enjoyable.
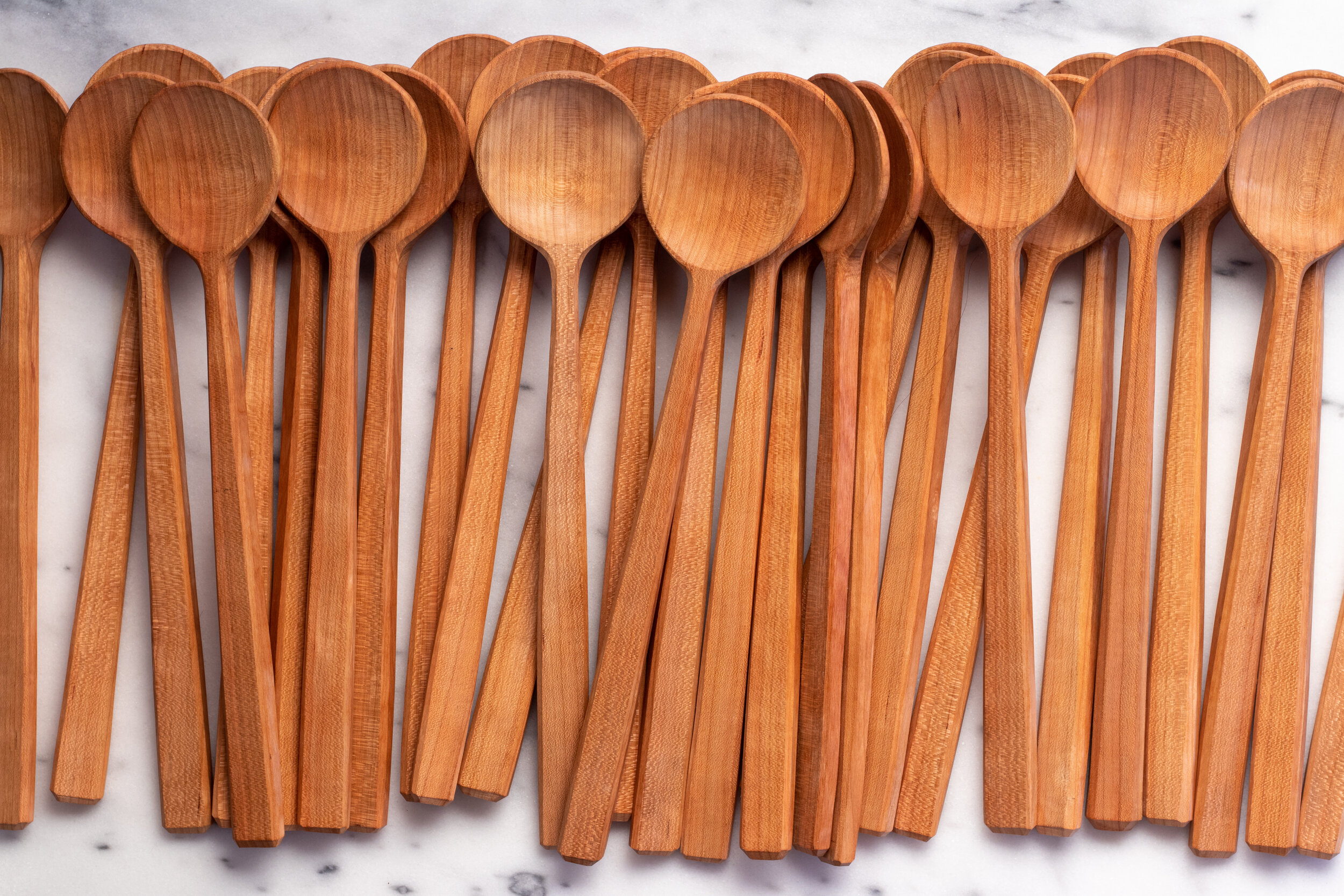
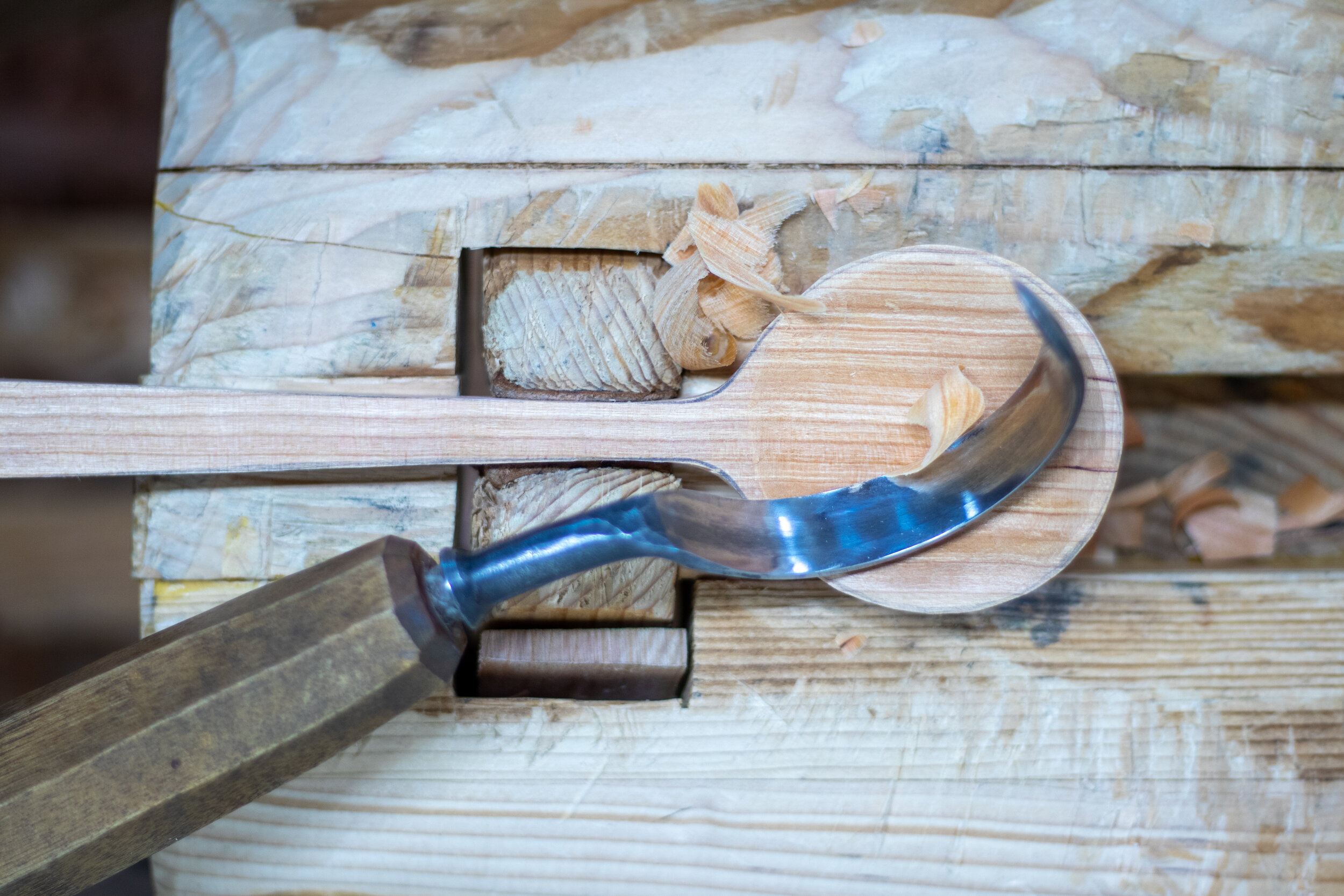